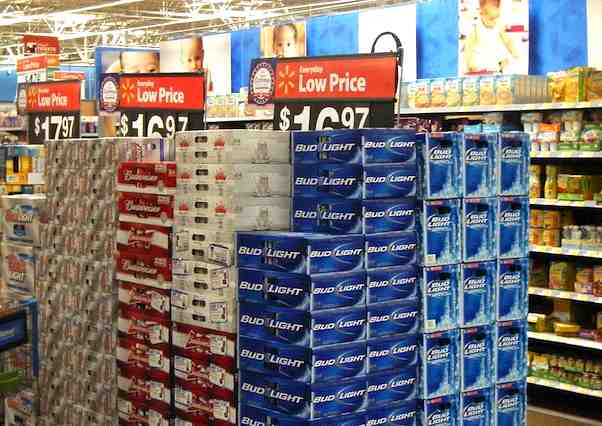
Walmart Inc.’s inventory management is one of the biggest contributors to the success of the multinational retail business. Considering the mammoth size of the company, effective and efficient inventory management is of critical importance in operational effectiveness. Walmart is known for cutting-edge technological applications for its inventory management aspect of operations. The company has perfected the art of innovating its inventory management methods and strategies. Thus, Walmart is an example of the benefits of advanced technology and innovation in optimizing inventory management performance. While there are a variety of other factors contributing to the success of this business, advanced inventory management is one of the core organizational capabilities that enable Walmart’s leadership in the global retail industry. This leadership establishes competitive advantages and the business strengths enumerated in the SWOT analysis of Walmart, relative to competitors, like Costco, Home Depot, Amazon and its subsidiary, Whole Foods, and other retail and e-commerce firms.
Walmart’s inventory management is a key success factor in the firm’s ability to grow to its current industry position as the leading retailer in the world. The company’s strategies for various business areas are linked to inventory management in terms of how strategic approaches support or exploit benefits brought through innovations in inventory activities. In this regard, such strategies applied in inventory management relate to Walmart’s operations management and productivity strategies.
Walmart’s Vendor-Managed Inventory Model
Walmart’s success in managing its inventory is partly due to the effective implementation of the vendor-managed inventory model. In this model, suppliers access data from the company’s information systems, such as data on current inventory levels and the rate at which certain goods are sold. Suppliers decide when to send additional goods to Walmart, while the company monitors and controls the actual transit of goods from warehouses to the stores. This strategy shifts some of the inventory control activities onto the side of the suppliers.
Walmart’s vendor-managed inventory has the benefit of minimizing delays in the movement of inventory across the supply chain. This benefit is achieved because suppliers can directly access current data about the inventory of their goods at Walmart stores. Another beneficial effect of using the vendor-managed inventory model is the minimization of costs in inventory management activity. The company does not need to spend for extra personnel to manage each supplier’s goods. Instead, this financial and human resource expense is directly passed on to Walmart’s suppliers.
Types and Roles of Inventory at Walmart Inc.
Walmart uses many types of inventory, each with a corresponding set of management approaches, strategies, and tactics. Each type fulfills a certain role in the retail company’s inventory and supply chain. The following types of inventory are some of the most notable in Walmart’s practices:
- Finished Goods Inventory
- Transit Inventory
- Buffer Inventory
- Anticipation Inventory
Finished goods inventory. The finished goods inventory type is the most significant in Walmart’s business. Finished goods arrive at the company’s stores. These goods are stored, and the inventory is replenished regularly. Thus, the role of this type of inventory is to support Walmart store operations, where the finished goods are moved from the company’s merchandise distribution centers to be sold to the retail buyers at the stores.
Transit inventory. Walmart uses the transit inventory type as the second most significant in supporting its retail operations. This type of inventory refers to the goods that are held while in transit. The global extent of Walmart’s supply chain means that some goods are in transit for days or weeks. The role of this inventory type is to support the replenishment of the finished goods inventory in the merchandise distribution centers and Walmart stores.
Buffer inventory. Walmart uses the buffer inventory type in its stores by keeping a small margin of extra goods in order to maintain business continuity when demand suddenly fluctuates. For this purpose, there will always be an extra stock of goods at Walmart stores. The role of this type of inventory is to ensure the adequate capacity of the company to satisfy sudden increases in demand, considering that current retail market prediction models may be accurate, but not perfect in modeling such fluctuations.
Anticipation inventory. Walmart uses the anticipation inventory type to ensure optimal capacity to satisfy consumer demand. This type is similar to buffer inventory because the company maintains extra stocks of goods to address an increase in demand. However, the anticipation inventory type is based on seasonal changes and corresponding empirical data on seasonal changes in the market. For example, Walmart dramatically increases its inventory size right before and during Black Friday to satisfy the massive increase in demand during this special shopping day. The company also uses anticipation inventory for the Christmas season and some long holiday weekends. Walmart does not use the anticipation inventory type during regular shopping days, which are the rest of the year. The role of this inventory type is to enable the company to satisfy expected seasonal increases in demand.
Just-in-Time Cross-Docking in Walmart’s Inventory Management
Walmart uses different methods to manage its inventory. Just-in-time inventory is the application of the just-in-time (JIT) method to inventory management. This method involves measures and activities for the operational objective of minimizing storage and related costs. At Walmart, the just-in-time inventory method is applied in the form of cross-docking. In cross-docking, suppliers’ trucks and the company’s trucks meet at the company’s warehouses or merchandise distribution centers. Goods are transferred from the suppliers’ trucks directly to Walmart’s trucks, which deliver the goods to the stores.
The main benefit of cross-docking at Walmart’s warehouses is the minimization of inventory size. Fewer goods are stored at the warehouses. A smaller inventory is less costly to maintain. Also, cross-docking enables Walmart to quickly deliver goods to the stores. This condition enables the firm to rapidly respond to fluctuations in demand and related changes in the market. Thus, this method of inventory management supports Walmart’s operational efficiency and business resilience.
Walmart’s Measures of Inventory Performance
Considering the size of its business and the variety of products it offers, Walmart uses numerous variables as measures of inventory performance. The following measures are some of the most significant:
- Inventory turnover
- Stock-out rate
- Inventory size
Inventory turnover is the rate at which Walmart’s inventory is sold out and replenished. It is a measure of the cost of keeping each item in stock. A higher inventory turnover rate is less costly and more desirable for the company. The stock-out rate is the frequency at which Walmart’s inventory becomes inadequate in satisfying demand. A lower stock-out rate is desirable. In addition, the company uses inventory size as a gauge of cost. As noted, the corporation spends less on a smaller inventory. These measures reflect the cost minimization objectives linked to Walmart’s cost leadership generic competitive strategy, which requires low costs to maintain attractive low selling prices.
Managing Inventory across Walmart’s Supply Chain
ABC Analysis. Category A items in Walmart’s inventory include the finished goods sold at its stores and operations equipment, such as information systems for supply chain management and inventory management. Items in this category are regularly monitored and recorded. Category B items in Walmart’s inventory are the other supplies or materials used for operations, such as maintenance equipment and office furniture. These items are moderately monitored and have moderate recording accuracy. Category C involves the least monitored and recorded inventory items, such as janitorial supplies and office supplies like paper. This category has the least impact on the company’s daily retail operations.
Inventory Information Systems. Walmart is known for its advanced information systems specifically designed to support international retail operations, including e-commerce operations. These information systems cover every area of the business. In inventory management, Walmart uses a system that allows suppliers to access data on the inventory levels of their products. This system supports the company’s vendor-managed inventory model, which helps minimize operating costs and enables the business to offer low selling prices.
Bullwhip Effect in Walmart’s Supply Chain. The bullwhip effect is the propagation of error in the form of inadequacy or excesses in the supply chain. A small error in one part of Walmart’s supply chain could lead to bigger errors and higher costs across the supply chain. The company minimizes the bullwhip effect in its supply chain through the vendor-managed inventory model. Vendor-managed inventory allows suppliers to directly access Walmart’s inventory data. In this way, the company’s personnel make a minimal contribution to errors in managing the movement of goods from the suppliers to the company’s stores.
Financial Impact of Walmart’s Inventory Management
Walmart’s vendor-managed inventory model minimizes the cost of managing inventory because some of the cost is transferred to the suppliers. The combination of the finished goods inventory, transit inventory, buffer inventory, and anticipation inventory supports the company’s cost leadership generic strategy through cost minimization. Walmart’s cross-docking as a form of the just-in-time inventory method also helps reduce inventory costs by minimizing inventory size. This combined approach supports the company’s profitability and financial soundness.
References
- Ada, E., Sagnak, M., Mangla, S. K., & Kazancoglu, Y. (2024). A circular business cluster model for sustainable operations management. International Journal of Logistics Research and Applications, 27(4), 493-511.
- Fahreza, F., Nurnabila, F., Riyadi, M. R., Muktyas, I. B., Murnaka, N. P., & Arifin, S. (2024, April). A systematic literature review: Analysis and improvement of Walmart supply chain. In AIP Conference Proceedings (Vol. 3024, No. 1). AIP Publishing.
- Hugos, M. H. (2024). Essentials of Supply Chain Management. John Wiley & Sons.
- Walmart Inc. – Form 10-K.
- Walmart Inc. – Location Facts.
- Vaka, D. K. (2024). Integrating inventory management and distribution: A holistic supply chain strategy. The International Journal of Managing Value and Supply Chains, 15(2), 13-23.