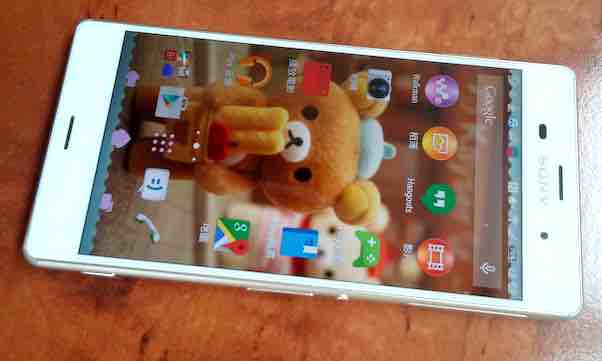
Sony’s operations in the consumer electronics, video game, entertainment, and financial services markets are guided through proactive productivity approaches in the 10 strategic decision areas of operations management (OM). These 10 strategic decisions pertain to the areas of concern to operations managers, with the aim of ensuring a streamlined business. This streamlining strengthens the competitive advantages noted in the SWOT analysis of Sony. The company’s operations management is based on time-tested approaches that support high efficiency in these business areas. As a major player in the global market, Sony maintains high productivity and performance with flexible operations management practices in these 10 strategic decision areas.
For the 10 decisions of operations management, Sony focuses on high efficiency, while integrating sustainability principles. These sustainability principles are central to Sony’s strategic organizational improvement. Successful operations management improves Sony’s performance relative to the market performance of consumer electronics, video games, and entertainment products of competitors, like Apple, Google (Alphabet), Samsung, Microsoft, and Nintendo, as well as Disney and Netflix. These companies create the strong competitive pressure described in the Five Forces analysis of Sony.
Sony’s Operations Management, 10 Critical Decision Areas
1. Design of Goods and Services. Sony designs its products for maximum business benefit. In this strategic decision area, operations managers aim to minimize cost, maximize quality, support operational sustainability, and optimize human resource utilization. Sony addresses these considerations through continuous improvement methods. These methods are intended to optimize all operations in terms of productivity and process efficiency. In addition, Sony’s generic competitive strategy of differentiation is applied through operations management approaches that emphasize optimal profitability alongside sustainability principles in product design. For example, the company’s iteration of PlayStation designs aims to capitalize on the production efficiency and market success of previous designs. In this regard, Sony adequately addresses the objectives in this strategic decision area of operations management.
2. Quality Management. Operations managers focus on quality standards and requirements as objectives in this strategic decision area. Sony’s operations management policy emphasizes the achievement of and support for kando, which is “emotional involvement” or the “power to stimulate emotional response.” Kando is a key factor highlighted in Sony’s mission statement and vision statement. This factor ensures products that capture customers’ attention and satisfy their expectations. For example, operations management efforts constantly search for solutions to enhance the quality of Sony’s products. These efforts support high operational productivity and the fulfillment of kando pertinent to this strategic decision in operations management.
3. Process and Capacity Design. Adequacy of production processes, related standards, and resource allocation is the objective in this strategic decision area of operations management. Sony addresses this objective through sustainability, which also helps streamline the business to satisfy market concerns regarding the environmental impact of business operations. For example, the sustainability of the company’s production processes helps minimize operational costs based on the minimization of resource requirements and production waste. In addition, Sony’s operations managers apply strategic decisions to maximize capacity utilization in production facilities, thereby leading to the maximization of productivity per facility.
4. Location Strategy. At Sony, operations management is concerned with distances from customers, suppliers, and resources. The objective in this strategic decision area is to optimize such distances to minimize operational costs, maximize revenues, and optimize market reach. In this regard, Sony’s marketing mix (4Ps) involves stores in high-traffic locations, such as malls and urban centers. This part of the marketing mix helps optimize the productivity of the company’s distribution and sales operations. Also, Sony’s e-commerce websites add to the effectiveness of the location strategy. For example, these websites inform customers about goods and services available at Sony Stores. Moreover, the company’s operations managers keep facilities productive through optimal location relative to the labor market and suppliers. Thus, for this strategic decision area of operations management, Sony minimizes overall average distances among facilities, resources, and markets to optimize business operations.
5. Layout Design and Strategy. The objective in this strategic decision area is to optimize the flow of resources, such as human resources, materials, and information. For this purpose, Sony’s operations managers monitor requirements for operational capacity, resources, and inventory. The highly productive flow of resources is achieved through an annual review of layout designs and strategies. For example, Sony’s operations management employs expert opinion and employee feedback to make decisions on current productivity issues linked to layout designs and strategies.
6. Job Design and Human Resources. The company’s objective in this strategic decision area is to develop adequate and high-performance human resources to support business operations and growth. Operations managers use Sony’s organizational structure (company structure) to facilitate HR development. For example, the corporate structure defines job designs that are specific to the business areas of the company, such as the consumer electronics business and the gaming business. On the other hand, Sony’s organizational culture (company culture) promotes high productivity and operational efficiency. For instance, the corporate culture’s emphasis on reliability requires job designs and HR programs that continually develop employees’ knowledge and skills. Comprehensive support for this organizational culture is included in Sony’s operations management for this strategic decision area.
7. Supply Chain Management. In this strategic decision area, operations managers’ objective is to maintain adequate supply to support current operations and business growth, especially in high-growth markets, with consideration for the market trends noted in the PESTEL/PESTLE analysis of Sony. The company fulfills this objective through automation and inclusive support for suppliers. Automation maximizes the productivity of Sony’s supply chain management activities. On the other hand, inclusive support for suppliers ensures suppliers’ growth and operational adequacy along with the company’s growth. For example, as suppliers grow with strategic support from Sony, their productive capacity continues to match the company’s growing supply needs. These efforts show that Sony reaches out beyond its organization to fulfill the objectives in this strategic decision area of operations management.
8. Inventory Management. Operations managers make strategic decisions on inventory ordering and holding to support operations while considering supplier capacity and customer satisfaction objectives. Sony’s approach involves centralized inventory management systems that enable management personnel to determine and update data on inventory levels and associated operational requirements. For example, as part of the company’s operations management standards, inventory managers must regularly check and update data pertaining to their respective facilities or areas of operations. Through such an approach in this strategic decision area of operations management, the resulting real-time data optimizes inventory and associated productivity variables at Sony.
9. Scheduling. The managerial objective in this strategic decision area is to maintain operation schedules that match resources and market demand. Sony’s operations managers use automated scheduling to achieve high productivity. For example, the company’s management systems provide real-time data on changes in operational needs. Sony’s managers use such data to apply appropriate changes in schedules. This factor supports optimally productive business processes. Sony also addresses issues on market variations through partial autonomy of some business activities. For instance, some of the strategic decisions in this area of operations management are made at the local or regional level, and others at the corporate level. Such partial decentralization of operational decision-making helps Sony achieve some degree of flexibility in responding to market variations.
10. Maintenance. Organizational reliability and operational stability are the objectives in this strategic decision area of operations management. Sony attains reliability in combination with sustainability. Sustainability is a core factor in efforts to improve the business, such as through Sony’s corporate social responsibility (CSR) and ESG strategy and stakeholder management. Sustainability initiatives contribute to the reliability of the firm’s operations and productivity. For example, such initiatives require maximizing efficiency, such as waste minimization. The resulting efficiency makes Sony reliable in terms of productive capacity. Furthermore, the company’s operations managers ensure stability through regular maintenance evaluation of resources, such as technologies and human resources. Corresponding changes are applied to Sony’s operations management activities in this strategic decision area.
Productivity at Sony
Sony uses different sets of criteria or metrics for productivity in its business areas. These sets are based on the needs of the consumer electronics, gaming, entertainment, and financial services businesses. The following are some of the metrics applicable to evaluating productivity in Sony’s operations management:
- Accounts processed per day (financial services productivity)
- Units sold per day (Sony Store productivity)
- Batches of materials processed per day (inventory management productivity)
References
- Fosso Wamba, S., Queiroz, M. M., Ngai, E. W., Riggins, F., & Bendavid, Y. (2024). The interplay between artificial intelligence, production systems, and operations management resilience. International Journal of Production Research, 62(15), 5361-5366.
- Sony Group Corporation – Businesses & Products.
- Sony Group Corporation – Form 20-F.
- Sony Group Corporation – History.
- Zhang, X., Denicol, J., Chan, P. W., & Le, Y. (2024). Designing the transition to operations in large inter‐organizational projects: Strategy, structure, process, and people. Journal of Operations Management, 70(1), 107-136.