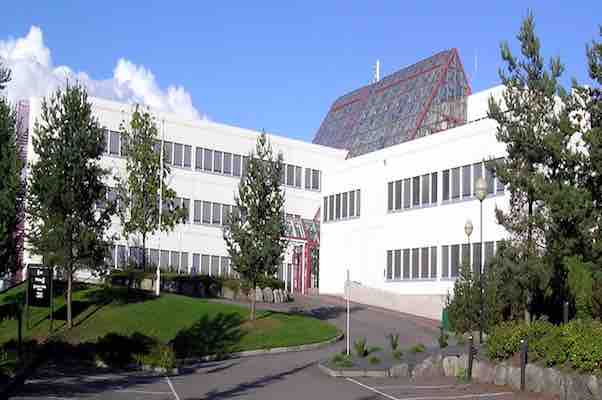
IBM (International Business Machines Corporation) has an operations management (OM) strategy for optimizing hardware and software development, distribution, and maintenance operations in the 10 strategic decision areas. Operations managers are concerned with the 10 decisions that strategically impact the success of the business. IBM implements policies and reforms through these 10 strategic decision areas to maximize the effectiveness of implementation while ensuring the continuity of operations. Also, Big Blue’s operations management fulfills its productivity goals by systematically addressing challenges and issues in each of these strategic decision areas. For example, each area is approached as a distinct component of IBM’s operations, although corporate managers address the operational goals of the business as an integrated whole. In this integrated and systematic approach, the company keeps its business productive and satisfies its strategic objectives. Thus, IBM’s continued success is significantly founded on sound operations management decisions that are relevant to current and emerging business needs.
IBM’s managers use operations management policies in the 10 strategic decisions to maximize productivity in all areas of the information technology business. For example, the company’s approach in the area of quality management requires operations managers to ensure the satisfaction of high-quality standards. Also, operations management personnel apply such policies to keep business processes productive. In relation, IBM’s operational efficiency depends on the effectiveness of human resource programs to maximize IBMers’ productivity.
IBM’s Operations Management Areas, 10 Decisions
1. Design of Goods and Services. This strategic decision area of operations management focuses on how to maintain consistently high quality within target cost limits for the company’s information technology products. For example, IBM’s operations managers look for methods to minimize cost fluctuations. These methods include continuous monitoring of operations to immediately solve problems. Considering the main strategic decisions emphasized in this area of operations management at IBM, such methods are on top of basic considerations for design specifications. For instance, managers implement design requirements and make the necessary allocations for cost, quality, and resources, while keeping productivity targets. In this way, the value and technological breakthrough aims in IBM’s vision statement and mission statement are fulfilled along with the satisfaction of operational objectives. Moreover, managers aim to integrate technological opportunities, such as the ones identified in the PESTLE/PESTEL analysis of IBM, into the methods implemented in this strategic decision area of operations management. The goal is to keep operations flexible enough for business growth opportunities, while adhering to design specifications and operational consistency requirements.
2. Quality Management. This strategic decision area of operations management has the objective of satisfying customers’ demands and expectations regarding IBM’s information technology products. In this case, the company’s operations managers employ regular quality tests to ensure compliance with quality requirements. For example, IBM’s operational standards are partly based on these quality requirements, while productivity objectives are established with allowance for conducting quality tests. Effective quality management contributes to competitive advantages over other technology firms, like Oracle, Hewlett Packard Enterprise, Microsoft, Google (Alphabet), Amazon, and Intel. As illustrated in the Five Forces analysis of IBM, these firms add to the strong competitive pressure in the industry.
3. Process and Capacity Design. High process efficiency and adequate production capacity are the objectives in this strategic decision area of operations management. IBM fulfills this objective through a continuous improvement model that integrates new operational standards and requirements in response to changes in the information technology market. Operations managers use IBM’s generic competitive strategy and intensive growth strategies for this model. The cost leadership generic strategy supports gradual but continuous improvement in productivity, process, and capacity maintained through the model.
4. Location Strategy. This strategic decision area of operations management aims for optimal locations in considering suppliers, customers, employees, and other components of the business, thereby impacting the place or distribution element in IBM’s marketing mix or 4P. This operational objective is addressed through strategies for online and non-online operations. For example, the company applies a traditional location strategy for non-online operations involving the manufacture, distribution, and sale of its information technology products. On the other hand, for online operations, IBM’s operations managers implement a centralized strategy that involves high-productivity work hubs or nodes that focus personnel, equipment, and related resources in a limited number of worldwide locations.
5. Layout Design and Strategy. High efficiency and productivity in the flow of information and resources are the objectives in this strategic decision area of operations management. IBM satisfies these objectives through a combination of automation and the use of standards and best practices in the information technology industry. For example, the company’s operations managers utilize industry best practices in layout design for manufacturing. On the other hand, IBM has operational standards for automating information flow throughout the organization, such as standards for real-time information on server usage and related statistics.
6. Job Design and Human Resources. The strategic decision in this area of operations management focuses on maintaining an effective workforce for the information technology business. IBM’s organizational structure (corporate structure) influences operational approaches used for this area. For example, human resource development programs are aligned with the specific functional requirements in the different segments or divisions of the organization. Also, IBM’s organizational culture (business culture) determines operations managers’ productivity methods, as well as the various approaches used in improving human resource capabilities, considering the need to maintain cultural support for innovation.
7. Supply Chain Management. Operations managers aim to keep high supply chain efficiencies and capacities in this strategic decision area. In this regard, IBM’s approach to operations management involves using information technologies to automate supply chain processes for high efficiency. This high efficiency supports economies of scale, which are one of the business strengths shown in the SWOT analysis of IBM. On the other hand, the company satisfies capacity goals through programs that support suppliers’ productivity growth. For example, these programs provide information and some technical support to help suppliers improve their operational capacities. This operations management approach aligns with efforts to address the interests of suppliers as stakeholders in IBM’s corporate social responsibility strategy.
8. Inventory Management. In this area of operations management, the strategic decision deals with maintaining adequate inventory while considering internal and external factors. For example, IBM must ensure adequate inventory despite challenges linked to vulnerabilities and risks facing firms in the information technology industry. The company has redundancy allowances and buffer inventory to address such operational issues and to account for fluctuations in market demand. Also, IBM’s operations managers achieve productivity objectives through inventory control based on real-time data on business processes and market needs and variations.
9. Scheduling. Appropriate schedules for processes and resources are IBM’s objective in this strategic decision area of operations management. The company’s scheduling approach is based on the type of operations, operational productivity requirements, and location of operations, among other variables. For example, IBM’s schedules for semiconductor development are different from the schedules for server maintenance and upgrades. In addition, operations managers at IBM use different sets of schedules based on geographic location to account for differences in the dynamics and business practices across markets and regions of the world.
10. Maintenance. This strategic decision area of operations management has the objective of maintaining adequate resources and processes to support the information technology business. For example, IBM maintains high productivity levels in its technology laboratories through regular checks and upgrades of relevant equipment. Such efforts ensure the adequacy of operational processes in the organization. In addition, operations managers implement a variety of programs to maintain the stability and growth of IBM’s resources, inclusive of human resources, as well as materials and equipment for corporate function and production processes.
Productivity Metrics at IBM
IBM uses different criteria for productivity, based on the area of operations, the type of operations, and the type of organizational output involved, among other operational factors. The company develops improvement strategies based on the results of productivity evaluations, which in turn are based on these criteria. In this case, the following productivity criteria are relevant to IBM’s information technology business:
- Server checks completed per week (maintenance productivity of IBM online services)
- Batches delivered per month (product distribution productivity)
- Accounts processed per year (IBM marketing productivity)
References
- About IBM.
- Cannas, V. G., Ciano, M. P., Saltalamacchia, M., & Secchi, R. (2024). Artificial intelligence in supply chain and operations management: A multiple case study research. International Journal of Production Research, 62(9), 3333-3360.
- IBM Strategic Partnerships.
- International Business Machines Corporation (IBM) – Form 10-K.
- Murthy, K. K. K., Khan, S., & Goel, O. (2024). Leadership in technology: Strategies for effective global IT operations management. Journal of Quantum Science and Technology, 1(3), 1-9.
- U.S. Department of Commerce – International Trade Administration – Software and Information Technology Industry.