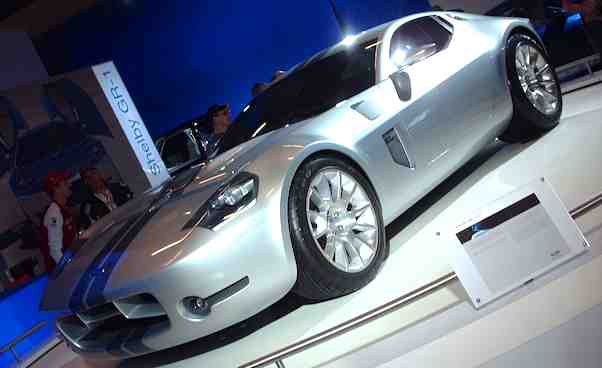
Ford Motor Company’s operations management (OM) optimizes the organizational processes of the multinational automotive business. Under the One Ford plan of former CEO Alan Mulally, the company’s operations management became more effective in addressing the 10 strategic decision areas. As one of the biggest firms in the global automotive industry, Ford maintains operations management strategies that deal with a variety of business conditions based on different market contexts. As such, in the 10 strategic decisions of operations management, Ford must ensure flexibility along with consistency throughout its global organization.
Ford’s 10 strategic decisions of operations management emphasize consistency and high productivity. The company maintains considerable flexibility to address business and regional automotive market variations. Through high productivity and efficiency, operations management helps address the tough competition illustrated in the Five Forces analysis of Ford. Competitive forces involve other automakers, such as Toyota, General Motors, Tesla, BMW, and Nissan.
Ford’s Operations Management, 10 Critical Decision Areas
1. Design of Goods and Services. Ford’s goal with this critical decision of operations management is global consistency in business and products. Ford’s mission statement and vision statement require such consistency. Consistency promotes the automaker’s financial effectiveness and ability to optimize customer satisfaction. Decisions in this area of operations management relate to Ford’s generic competitive strategy and intensive growth strategies, which value product innovation. The company’s automobiles, accessories, and financing services are designed to be differentiated from competing products in the international automotive market.
2. Quality Management. This strategic decision area of operations management concerns the satisfaction of quality expectations regarding cars and trucks. Ford Motor Company does so through standard quality assurance practices. The firm also conducts random batch tests on its products to ensure quality. Quality evaluation also involves data that the company acquires through market research to identify customers’ quality expectations about automobiles and related services. Ford’s company culture (work culture) maintains a mindset of quality in human resources, in support of the quality standards and measures in this area of operations management.
3. Process and Capacity Design. This strategic decision area of operations management supports production goals. Ford pioneered the assembly line method, which maximizes production capacity. Also, the automaker continues to improve its capacity by developing new facilities for its production network and supply chain. The high efficiency and high productivity of business processes are among the main factors that reinforce the business strengths and competitive advantages noted in the SWOT analysis of Ford Motor Company. With support from decisions in this area of operations management, such strengths enable the company to withstand the aggressiveness of other large multinational automakers.
4. Location Strategy. Ford Motor Company’s aim in this strategic decision area of operations management is to ensure the strategic benefits of its facility locations. The company’s strategy involves regional production facilities, such as car factories in Germany. On the other hand, dealership locations are based on market size and proximity to target buyers. Ford’s marketing mix (4Ps) relates to this area of operations management, in terms of selecting locations for maximum market reach and vehicle sales.
5. Layout Design and Strategy. In this strategic decision area of operations management, the objective is to maximize the productivity and efficiency of workflows and resources. Ford addresses this objective through automation of production processes, such as through the use of robotics in production facilities.
6. Job Design and Human Resources. Ford has the goal of maximizing human resource effectiveness and efficiency in this strategic decision area of operations management. Ford’s corporate social responsibility (CSR), ESG, and stakeholder management programs support HR capacity and employee satisfaction. The company ensures continuous improvement and personnel development in its strategies. The teams and divisions in Ford’s company structure (business structure) determine the factors influencing operations managers’ critical decisions for optimizing workforce productivity.
7. Supply Chain Management. This strategic decision area of operations management focuses on streamlining and cost-effectiveness in the supply chain. Ford’s supply chain is global and involves company-owned production facilities, as well as third parties. The company-owned facilities, such as those in the Ford River Rouge Complex in Michigan, are a result of the company’s backward vertical integration strategy. This strategy empowers Ford to control the supply of some of the materials used for manufacturing its vehicles. However, the trends, opportunities, and threats noted in the PESTLE/PESTEL analysis of Ford affect such operational control and the operating condition and productivity of the supply chain.
8. Inventory Management. Ford’s inventory management supports just-in-time manufacturing methods, which require continuous monitoring to adjust the inventory and minimize its costs. However, in this strategic decision area of operations management, Ford’s actual inventory management performance also points to market-based inventory decisions. Different markets present different challenges, and the automotive company applies different inventory management practices to suit relevant market variations.
9. Scheduling. In this strategic decision area of operations management, the short-term and intermediate schedules of processes and resources are considered. Ford addresses these concerns through automated scheduling in its production facilities, and semi-automated scheduling in its offices, such as corporate offices and regional offices.
10. Maintenance. The goal in this strategic decision area of operations management is to maintain adequate business processes to satisfy demand. Ford addresses this goal through a combination of strategies for HR, IT, manufacturing and other areas, as well as maintenance teams for facilities and other assets.
Productivity at Ford Motor Company
Ford Motor Company’s operations management addresses productivity goals for the 10 strategic decision areas. Since the firm has various operations and products, a wide array of productivity measures and metrics is used. Some of Ford’s productivity metrics are as follows:
- Number of service jobs completed per day (after-sales service productivity)
- Number of cars and trucks rolled out per day (manufacturing productivity)
- Number of applications processed per day (Ford Motor Credit Company productivity)
References
- Ford Motor Company – Form 10-K.
- Ford Motor Company – Operations.
- Ford Motor Company – Sustainability.
- Gauss, L., Lacerda, D. P., Siluk, J. C., & Romme, A. G. L. (2025). Design science in operations management: A review and synthesis of the literature. International Journal of Management Reviews, 27(2), 221-237.
- Hughes, C. (2025). The assembly line at Ford and transportation platforms: A historical comparison of labour process reorganisation. New Technology, Work and Employment, 40(1), 41-59.
- Sajko, T., Koch, V., Treul, S., Pacher, C., & Zunk, B. M. (2025). Identifying competences of engineers in the context of operations management: A literature overview. Procedia Computer Science, 253, 1760-1769.
- U.S. Department of Commerce – International Trade Administration – Automotive Industry.