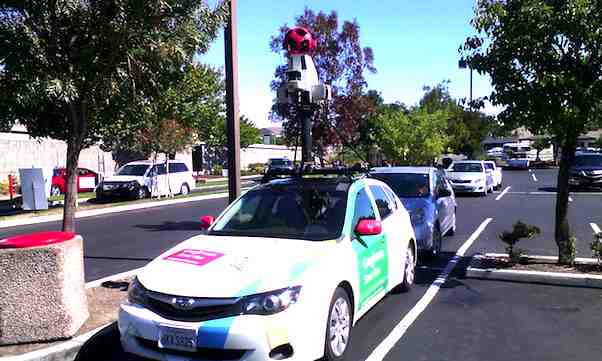
Google (Alphabet) applies strategic decisions in operations management for optimal innovation and productivity. This business condition promotes efficiency and high productivity in innovating information technology products. Google’s operations management involves strategic goals that match the 10 strategic decisions of Alphabet Inc.’s operations management and productivity approaches. The effectiveness of core competencies in operations management affects how the technology and online service company fulfills its strategic goals and objectives. In this regard, the 10 strategic decision areas of operations management contribute to the achievement of strategic goals based on Google’s (Alphabet’s) mission statement and vision statement. Managers’ decisions in these areas relate to productivity rates and human resource management, which determines options for fulfilling the mission and vision of Google and other Alphabet subsidiaries, including Google DeepMind and Waymo.
Google satisfies the objectives of the 10 decision areas of operations management in its business activities. These 10 decision areas contribute to the technology corporation’s productivity and organizational success. For example, Google’s product design process relates to the “design of goods and services” decision area of Alphabet, as well as other decision areas of operations management, such as quality management (keeping consistent product quality) and job design and human resources (ensuring sufficient human resources for production). In these strategic decision areas, Alphabet maintains effective and efficient operations that fulfill productivity and profitability objectives.
10 Strategic Decision Areas of Operations Management at Google (Alphabet)
1. Design of Goods and Services. This decision area focuses on Alphabet’s product specifications and related variables, such as operating cost limits, quality standards, and resource requirements. For example, the design of Google’s online search service determines the technological assets and human resources needed in operations management, to support algorithm design and development. Product design affects all the other strategic decision areas of Alphabet’s operations management, such as quality management and human resources. To keep business processes productive, this decision area adapts to budget limits, such as for developing new mobile apps. Also, Google’s (Alphabet’s) generic competitive strategies and intensive growth strategies are implemented alongside the design specifications of goods and services.
Market research data, including analytics from Google’s services, are among the inputs for this strategic decision area of Alphabet’s operations management. Google’s services generate big data from users. Such data can be anonymized and aggregated to provide information about the products and features that work and those that do not. Market research informs Alphabet’s corporate decisions in this operations management area, for product design and the strategic direction of subsidiaries, like DeepMind, Google, and Google Fiber.
The design of goods and services relates Google’s operations management to the competitive landscape. The company’s products compete with information technologies and online services from other companies. For example, Google’s products compete with the consumer electronics of Microsoft, Apple, Samsung, and Sony; the online advertising services of Facebook, eBay, and others; the video streaming services of Disney, Amazon, and Netflix; and the Internet services of Verizon. Many of these companies also compete with Google in multiple markets and industries. For instance, Amazon and Microsoft also compete in the cloud computing services market. These competitors affect Alphabet’s product design. Thus, the competitive landscape influences this strategic decision area of operations management at Google.
2. Quality Management. This operations management decision area deals with satisfying quality standards, based on Alphabet’s business strategies and customer expectations. As one of the world’s biggest information technology businesses, the company has high quality standards to ensure market leadership. Google’s operations management involves quality requirements for advanced technologies for its online services and consumer electronics. In quality management applications, Google uses iterative testing, debugging, and innovation. User involvement and feedback, reviews, and error reports inform the direction of quality enhancements at Google and other subsidiaries of Alphabet Inc. These activities minimize bugs in software products and enhance operational productivity.
Successful quality management leads to high productivity and product quality, which add to the business strengths identified in the SWOT analysis of Google (Alphabet). Quality standards and productivity targets influence the competitive advantages of the company’s goods and online services. For example, this strategic decision area of operations management at Alphabet Inc. ensures that Google Fiber effectively competes with Internet service providers, such as Verizon and Comcast. Similarly, quality management supports Google’s competitiveness against technology companies with artificial intelligence and cloud services. Furthermore, quality management in Google’s operations management reinforces the company against the competitive force of other digital service providers and software developers. Thus, decisions in this operations management area relate to Alphabet’s corporate strategies for managing competition in information technology and online service markets.
3. Process and Capacity Design. In this strategic decision area, Google’s operations management deals with the production processes for goods and services. The objective is to optimize the productivity and capacity of these processes through adequate resource allocation and management support involving Alphabet’s corporate headquarters and other relevant management levels of the technology business organization.
For Google’s web-based and software products, this decision area of operations management maintains almost the same number of workers even if demand for these products increases. Web-based or software products are easily distributed through the Internet without significantly impacting Alphabet’s human resource capacity. Capacity design is addressed at Google through standardized processes in software development.
For tangible goods, like Pixel smartphones and Chromecast dongles, this operations management decision area has a bigger impact because of the physical nature of the products and production processes. For example, Alphabet applies process and capacity design in prototyping and in contract manufacturing. Google develops its Pixel devices but outsources production to equipment manufacturers. Thus, the operations management and productivity of these manufacturers affect the process and capacity design of Google.
The technology and online services company’s process and capacity design relates to other firms in terms of competition. Through Google’s efforts to make its own chips for high capacity and process productivity, Alphabet imposes a competitive threat to microchip and semiconductor companies, such as Intel. Also, the process and capacity design of Google’s digital advertising network influences its competitiveness against other online ad services, such as Facebook’s and eBay’s. Thus, this strategic decision area of Alphabet’s operations management is a factor in building competitive advantages.
4. Location Strategy. Decisions in this area of operations management cover the locations or venues that Google uses. The strategic objective is to effectively and efficiently reach customers and resources, including hardware engineers and material suppliers. Location options and decisions relate to the place component of Google’s (Alphabet’s) marketing mix or 4P. For Google’s web-based digital products, this operations management decision area focuses on delivering products to customers through Internet-based interfaces, including websites and mobile apps. Alphabet maintains facilities around the world, such as offices in California and Singapore. These offices provide online customer support and other services. For goods, such as Chromecast and Pixel devices, this decision area of operations management involves networking with suppliers and manufacturers. Google’s supply chain spans multinational trade routes that take advantage of overseas factories’ low labor costs and high production capacities, which affect outsourced productivity and Alphabet’s productivity.
5. Layout Design and Strategy. The goal in this operations management area is to efficiently move resources and information throughout Alphabet’s business organization. At the company’s data centers, layout design affects process productivity in inventory management and other areas of data center operations management. In the case of Google, Alphabet’s layout design and strategy involve workplaces that are designed to motivate employees’ creative and innovative workflows at Googleplex in California. In developing web-based and software products, the company combines efficiency and creativity to optimize productivity. Google’s (Alphabet’s) organizational structure (company structure) defines the layout requirements in this strategic decision area of operations management.
6. Human Resources and Job Design. The objective in this strategic decision area is to plan and maintain an effective workforce through job designs that support all areas of Google’s business. The operations management purpose is to ensure adequate human resource support for the technology business and its strategic goals. Human resource management programs and initiatives at Google recruit and retain workers, and train and specialize human resources for optimum performance for the needs of the technology company and its businesses. The company emphasizes smartness and excellence in its human resource development, to support excellence in technological innovation. Alphabet also has competitive compensation packages designed to minimize employee turnover at Google, Waymo, DeepMind, and other subsidiaries. Incentives, benefits, and high salaries are necessary, considering the labor force competition with Microsoft, Apple, Amazon, and other firms. Also, Google’s (Alphabet’s) organizational culture (company culture) influences the suitability of job design in terms of alignment with workplace culture and related expectations among workers.
7. Supply Chain Management. This strategic decision area of Google’s operations management has the objective of keeping adequate supply that matches the needs of the information technology business organization. Productivity objectives are satisfied through successful supply chain management, which supports Alphabet’s business processes, like prototype development and office personnel’s activities. The company uses advanced information systems to manage its supply chain. The business analyzes inventory records to forecast demand, and to advise suppliers and equipment manufacturers. Also, Google’s (Alphabet’s) corporate social responsibility strategy and stakeholder management programs inform this area of operations management in addressing the concerns of suppliers as a stakeholder group.
Suppliers have weak bargaining power over the business, as explained in the Five Forces analysis of Google (Alphabet) using Porter’s model. Suppliers weakly impact the company’s operations management, considering the company’s size and the options it has for its information technology supply chain. Also, the industry and market trends identified in the PESTLE/PESTEL analysis of Google (Alphabet) shape the company’s supply chain decisions. Such factors show that this strategic decision area of the online services and consumer electronics company’s operations management is subject to external influences.
8. Inventory Management. Google’s objectives in this area of operations management include adequate inventory levels, minimal wastage, and minimized inventory expenses. Strategic decisions select different inventory types appropriate to the technology business. For example, Alphabet’s inventory management for Google involves automation to monitor and control inventory, especially in managing inventory for web-based and software products. Schedules and supplier capabilities in this operations management area determine the stability of equipment supply, and the availability of server components for data centers.
9. Scheduling. The strategic decisions that Alphabet makes in this area of operations management streamline short-term and long-term schedules to match current and expected business needs. For example, scheduling the release of new Pixel devices matches expected market demand, for optimal productivity, product distribution, and sales. Google’s operations management takes advantage of automation for monitoring business processes and productivity levels. Also, to support creative innovation, Alphabet has flexible schedules in some areas of its business, such as at Google workplaces.
10. Maintenance. In this decision area of operations management, the objective is to keep the stability and reliability of Alphabet’s business processes. To maintain competitive and successful Google operations, the company continually updates its information systems, servers, and software. The company’s operations managers and support teams keep abreast of current operational problems and disseminate such information in the organization to enable Google’s high productivity.
Productivity in Operations Management at Google (Alphabet)
Alphabet Inc. has a diverse set of operations representing various products. As a result, productivity criteria vary, depending on the subsidiary and the goods or services involved. Some of the productivity criteria or metrics applicable to Google’s operations management are as follows:
- Rate of software error or bug correction – This metric measures the productivity of Google’s software development personnel and their teams.
- Rate of release of mobile app updates – This productivity criterion matches current information technology trends, and measures Alphabet’s operations management effectiveness in supporting product development and rollout.
- Stockout rate – This productivity metric is general but applicable to Alphabet. The stockout rate reflects the productivity of personnel and processes in inventory management, and the productivity of the information technology company’s supply chain.
References
- Alphabet Inc. – Form 10-K.
- Alphabet Inc. – Investor Relations – ESG.
- Fosso Wamba, S., Queiroz, M. M., Ngai, E. W., Riggins, F., & Bendavid, Y. (2024). The interplay between artificial intelligence, production systems, and operations management resilience. International Journal of Production Research, 62(15), 5361-5366.
- Google Supplier Code of Conduct.
- Google Sustainability – Accelerating the Transition to a Circular Economy.
- Nzeako, G., Akinsanya, M. O., Popoola, O. A., Chukwurah, E. G., & Okeke, C. D. (2024). The role of AI-Driven predictive analytics in optimizing IT industry supply chains. International Journal of Management & Entrepreneurship Research, 6(5), 1489-1497.
- Rikap, C. (2024). Varieties of corporate innovation systems and their interplay with global and national systems: Amazon, Facebook, Google and Microsoft’s strategies to produce and appropriate artificial intelligence. Review of International Political Economy, 1-29.